The RL10 rocket engine, a stalwart in area exploration for practically sixty years, is present process a major improve by way of additive manufacturing. Aerojet Rocketdyne, the engine’s producer, is leveraging 3D printing to reinforce the engine’s performance and manufacturing effectivity. This improvement marks a brand new part within the RL10’s illustrious historical past, which started in 1962.
The most recent iteration, dubbed the RL10C-X, is ready to debut on a Vulcan rocket in 2025. This new variant goals to considerably cut back prices and enhance manufacturing capability. Whereas the present RL10C mannequin, utilized in ULA’s Atlas V and shortly the Vulcan rocket, incorporates 3D printing for its injector plate, the RL10C-X will broaden this software to your complete thrust chamber. These developments are anticipated to yield extra environment friendly efficiency.
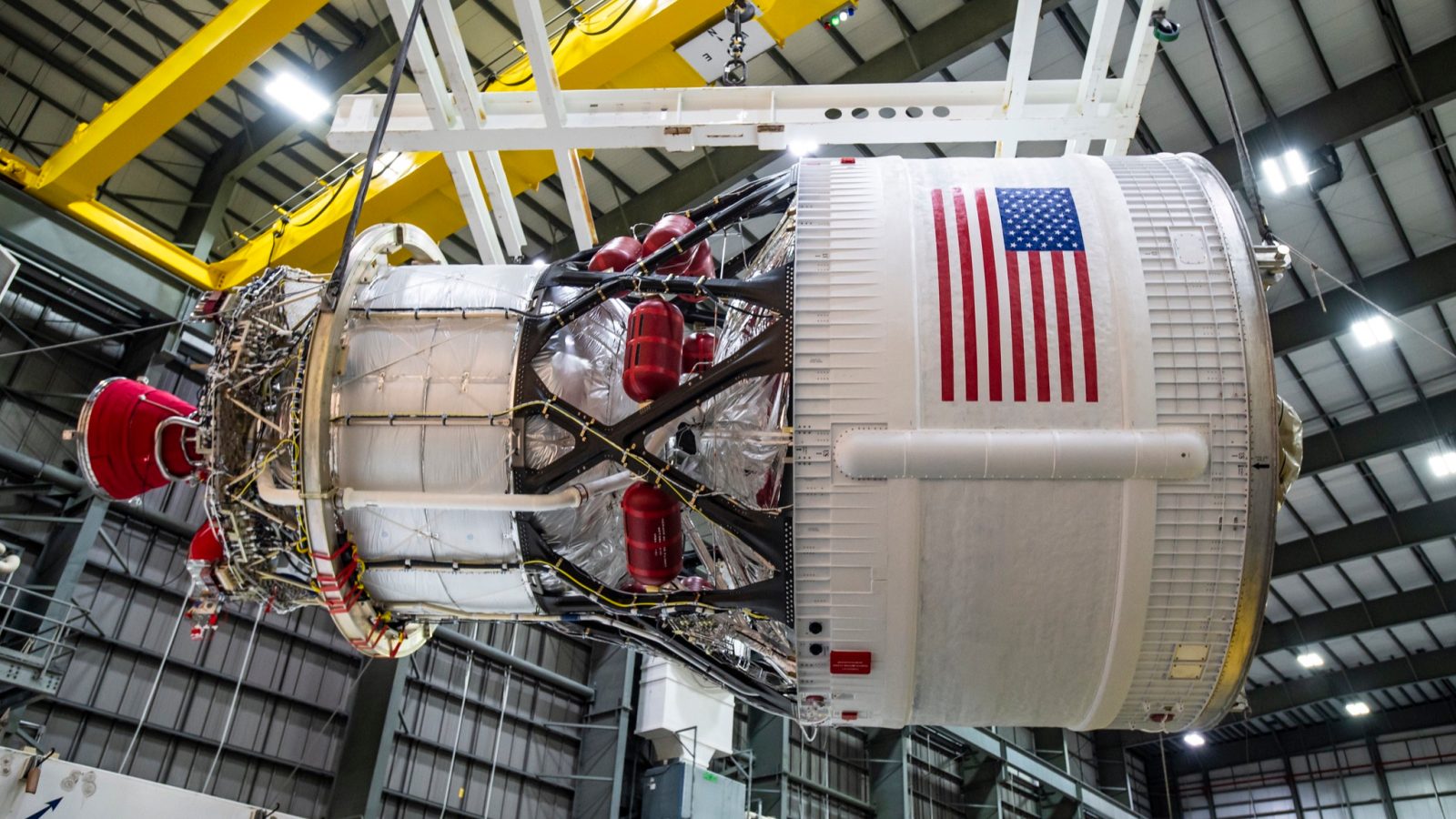
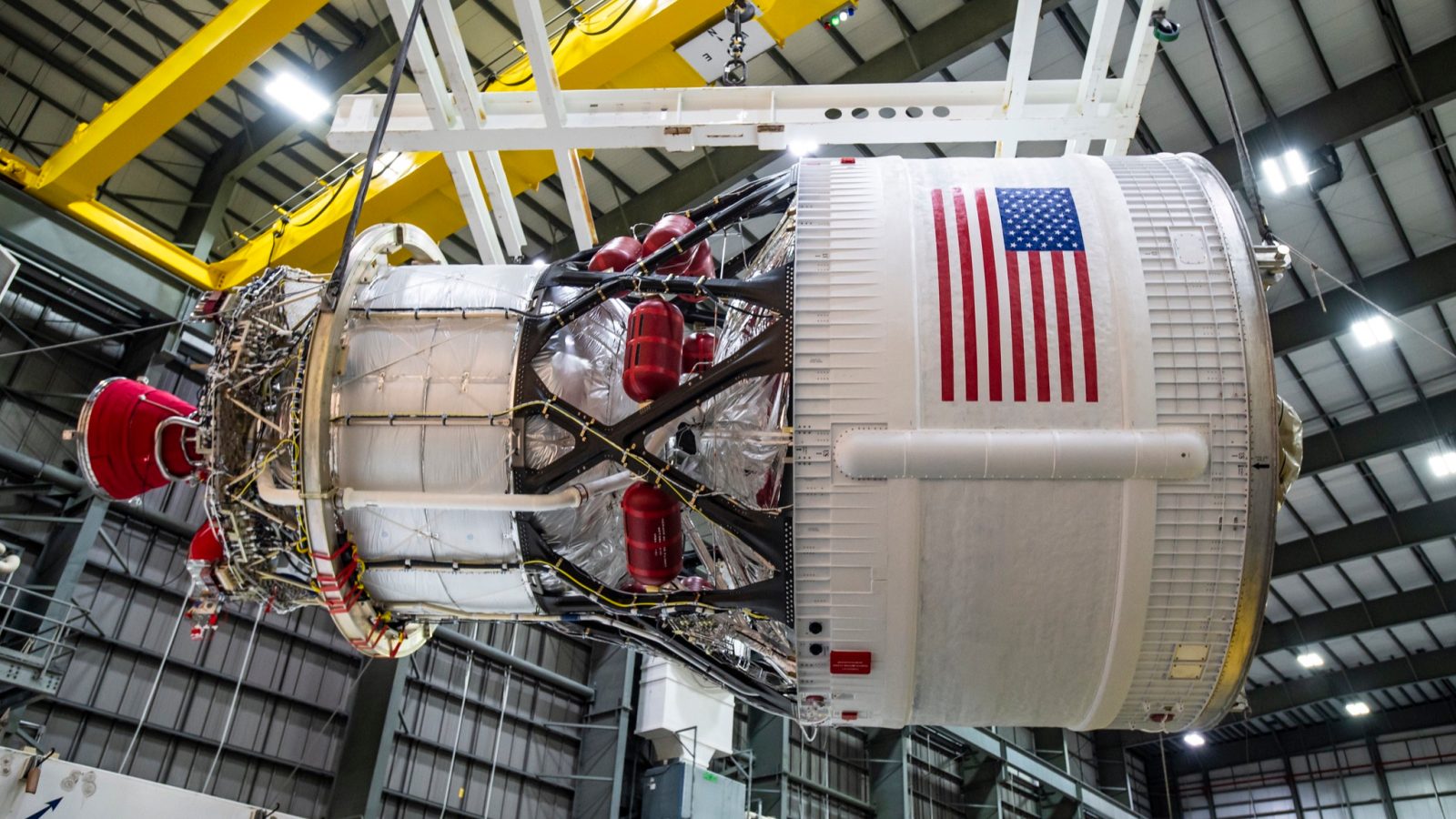
Aerojet’s manufacturing of the RL10 can be set to extend, rising from 16 models yearly to probably 40, to fulfill the calls for of varied area missions, together with the Atlas V, Vulcan, and Artemis packages. This enhance aligns with the corporate’s technique to reinforce the engine’s capabilities and manufacturing course of.
Traditionally, the RL10 has been a pioneering engine within the U.S., being the primary to make use of hydrogen and oxygen with an expander cycle. Its main software has been within the Centaur second stage on Atlas and Titan rockets, and it is usually part of the Delta IV’s higher stage and NASA’s House Launch System. The engine’s design has remained largely unchanged over the many years, showcasing its enduring reliability and effectiveness in area journey.
Supply: spaceexplored.com
Come and tell us your ideas on our Fb, X, and LinkedIn pages, and don’t overlook to join our weekly additive manufacturing e-newsletter to get all the newest tales delivered proper to your inbox.